Arrow’s assemblies have high-atmosphere applications that must be closely monitored with various sensors and cycled at a variety of extreme conditions. DMC developed a LabVIEW driver for the servo motor drive (Kollmorgen AKD2G) to control the motor via Modbus commands. This gives the application the ability to change the speed, reverse, or home the motor based on measurements from the external sensors. The test application takes the PBNAs through a vacuum test to ensure they are flight ready before launching to space on a rocket. In space, a robotic arm will tighten down the assemblies, so the PBNAs must tighten down to full tensile stress without exceeding the torque limits of the robotic arm. The test application runs up to four assemblies in parallel, taking them through hot, cold cycles as well as vacuum tests to ensure they won’t fail while in space. The driver establishes two-way communication with the drive so the state of the motor can be monitored and logged as well.
The application utilized two DMC tools to meet project requirements and cut down on engineering time. The state-machine based SequencerLite provided a flexible solution to cycle multiple assemblies simultaneously via cloned Sequencer instances.
DMC Template Project
The DMC Template Project is a newly developed tool that reduces development overhead and provides infrastructure for object-oriented programming in LabVIEW. The DMC Template Project features an HMI framework that is easily modified and comes out of box with alarm handling and a settings page. The settings are used to preserve variables through application executions, which is useful for set-and-forget variables like hardware connection or device specific parameters.
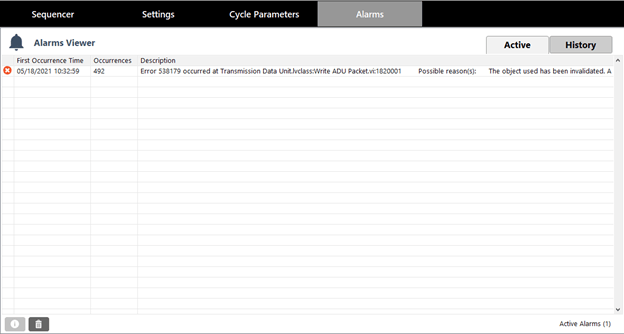
The UI of the tester was designed to present the operator with the most information and control over each assembly in an organized fashion. The main panel is partitioned into four sub-panels which control their respective assembly. Each sub-panel allows the operator to select the desired cycle parameters from a pre-configured list, then run and abort the cycle. There is also a live updating chart with tabs that display the force/torque and motor data, thermocouple data, and configure the home position of the servo motor.
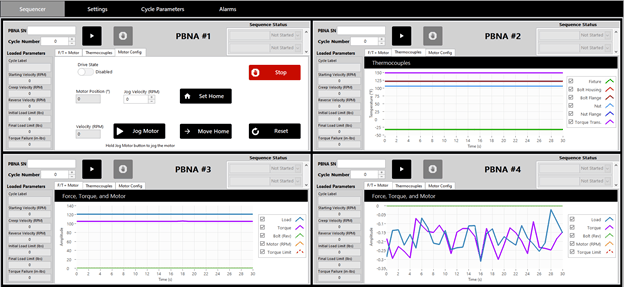
Learn more about DMC’s LabVIEW Programming expertise and contact us to get started on your next project.