DMC designed, developed, commissioned, and supported the SCADA system for a battery cell and module line.
The main functionalities of the system include:
- Communication and control interface between SAP and the line equipment.
- Collected data from the equipment and sent it to SAP.
- Retrieved recipe information from SAP and sent it to the equipment.
- Interfaced with the line equipment which included a mix of devices such as PLCs, torque tools, custom applications, etc.
- High fidelity data collection that resulted in of a large amount of data per battery module
- High resolution image collection from multiple vision inspection systems
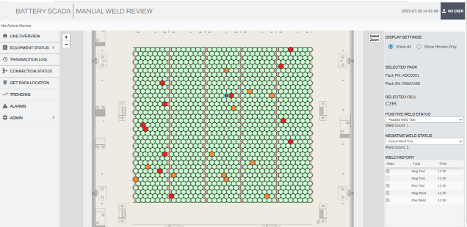
Figure 1-weld review. Shows a high-level view of which cells in the module have failed. Allows the user to click on a cell to get more information.
DMC joined the project during the design phase to advise on the overall architecture between the SAP and controls layers. SAP PEO was a novel platform without a standard method to talk to machine devices, so the client sought a partner with experience integrating complex systems. DMC worked with the client on designing the system and developing functional specifications which included defining the specific message structures for passing data between all systems.
Once the specifications were complete, DMC developed the code offline. Getting an early start on development offline enabled us to meet a tight deadline. As a part of the project process, we held weekly check-ins with the client to review the project status and demonstrate the software via simulation to keep a tight feedback loop on development. DMC also worked closely with the SAP development team to ensure the two systems would communicate seamlessly once deployed. This included multiple rounds of UATs, weekly check-in meetings, and quality checks.
When offline development was complete, DMC went onsite to the customer’s facility to successfully commission the system and perform operator training. DMC’s flexible code structure and robust logging systems made it easy to test the live system and make last-minute changes, resulting in an on-time SCADA acceptance test.
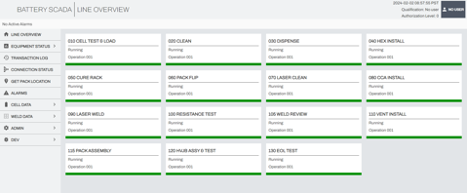
Figure 2-line overview. Shows the status of each station in the line.
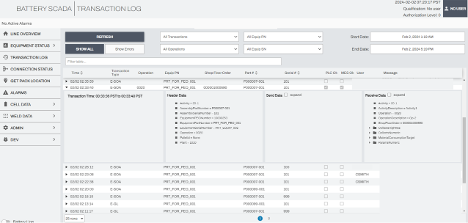
Figure 3-transaction log. Shows a detailed summary of the communication between SAP and the PLCs.
Learn more about DMC’s Ignition programming expertise and contact us with any inquires.