This MES project implemented a comprehensive enterprise solution across multiple sites for anode, cell, and module lines. Each of the sites had its own on-premise Ignition and Sepasoft server, which collected data from the lines both manually and automatically. This enabled the MES to have full material traceability throughout all the plants by leveraging Sepasoft’s enterprise capabilities to send traceability data between sites. The MES also sent traceability data through MQTT up to Snowflake for further analysis. This allowed the quality and process teams to obtain valuable data to help inform process improvements.
On top of the traceability of data throughout the system, DMC also implemented Sepasoft’s SPC module to add quality functionality to the system. The quality features were very configurable and allowed the quality users to enable and disable verifications and set the limits of different verifications. This allowed for the quality team to have greater control and flexibility of when parts were put on MRB hold as the manufacturing processes changed.
DMC partnered with the client through a staff augmentation model where DMC engineers collaborated closely with the client’s internal developers. Using this approach, the client was able to maintain the system themselves while leveraging DMC's technical expertise to assist with complex architecture. DMC’s support also ensured that the substantial development workload was completed on schedule.
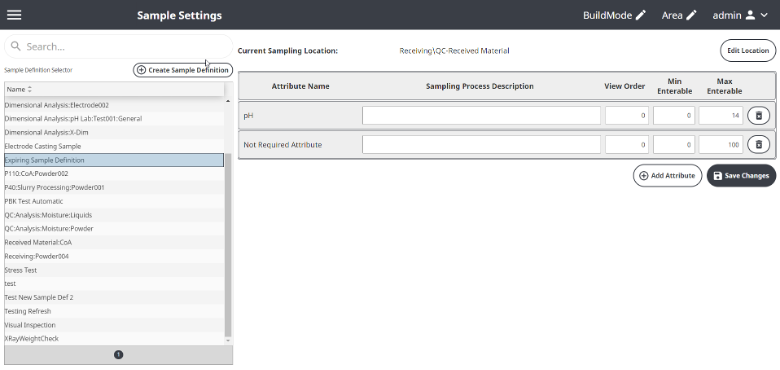
Figure 1 - Quality team screen where users can create new sample definitions
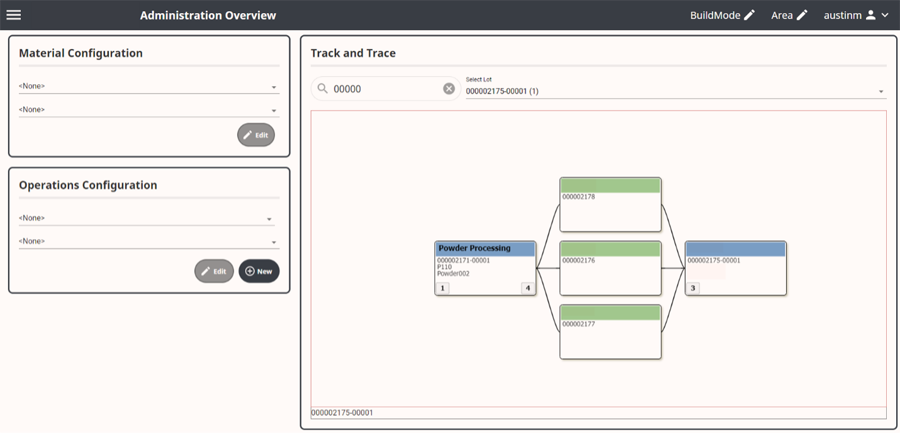
Figure 2 - Track and trace of material through the process
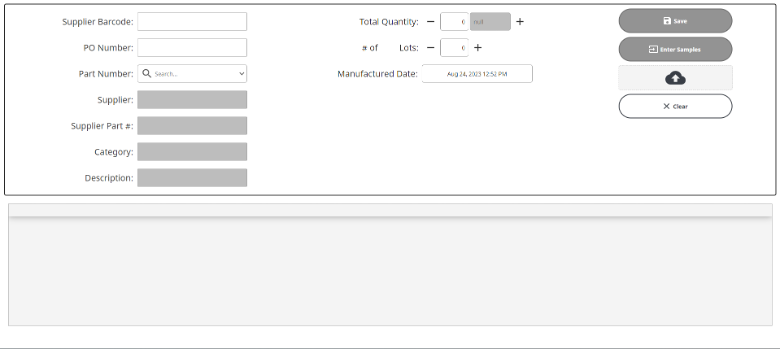
Figure 3 – material input screen where the user can receive materials and log data for that material
Learn more about DMC’s Sepasoft Programming expertise and contact us for your next project.