With the release of Siemens TIA Portal V14, and even more recently V14 SP1, DMC has been able to develop larger, more complex applications within one development environment which used to require two or more development environments (ex. TIA Portal with SIMOTION SCOUT for motion control applications).
While many improvements have been made recently to allow for more technically sophisticated controls systems to be developed exclusively within TIA Portal, DMC has run into some limitations.
One such "Gotcha!" to be aware of applies to the Siemens TM Timer DIDQ Modules. The high speed I/O functionality of the module is currently only available when it is mounted on a remote head module. When configured as local I/O (as shown on the front page of the device manual, below for reference), the module cannot be utilized in applications that require precise time resolution such as Measuring Inputs and Output Cams.
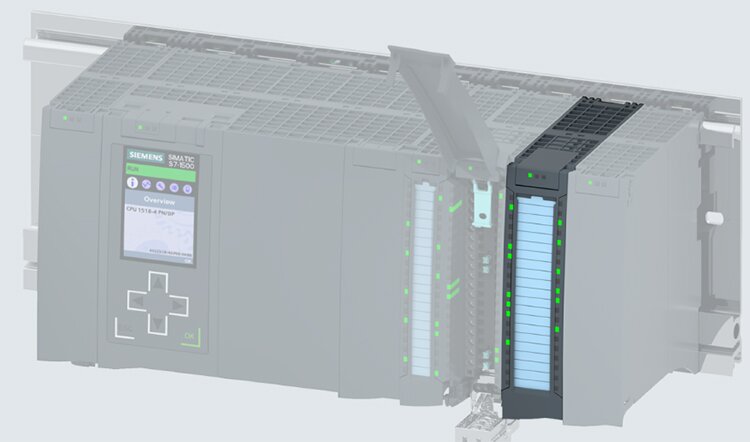
However, when used in a distributed I/O system (i.e. in conjunction with an ET200MP or ET200SP module), the two modules can be used in many ways to solve applications such as:
- Electronic cam controller (in conjunction with an application example)
- Length measurement at a constant speed
- Pulse output with a defined length
- Precise time capturing of an input edge
- Precise time outputting of an output edge
- Counting up to 50 kHz
- Counting of 2 phase-shifted signals with quadruple evaluation
- Outputting of a pulse-width modulated signal (PWM)
-
- Reading and outputting of bit patterns by 32-fold oversampling
You can also use this hardware configuration to provide high-speed I/O for Technology objects such as Measuring Inputs, Output Cams, Cam Tracks, and High-Speed Counters.
The remainder of this post will focus on the differences between using a TM Timer DIDQ Module Locally versus on a Remote Rack.
TM Timer DIDQ Module as Local I/O
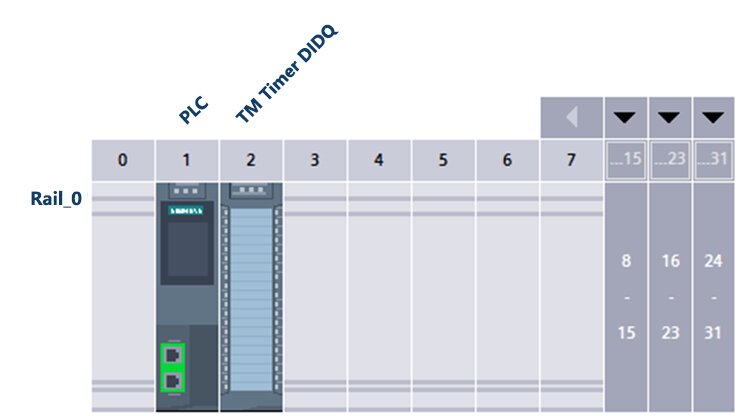
The limitations of the timer modules when configured locally stem from the way the CPU communicates with the I/O module. When mounted on a local rack, the backplane is used for communication. And while it may seem like the CPU is capable of communicating at IRT (Isochronous Realtime) speeds, this is only true when the hardware is configured as a Profinet device.
Under the Limiting conditions for the applications of the module Siemens notes, "Time-stamped IOs and oversampling require an isochronous mode of the module and the CPU and thus Profinet IO with IRT for fast synchronous communication."
If you are only looking to use the counting and/or PWM features of the modules, you are in luck! In these scenarios, you can use the module either on the local rack or on a remote rack.
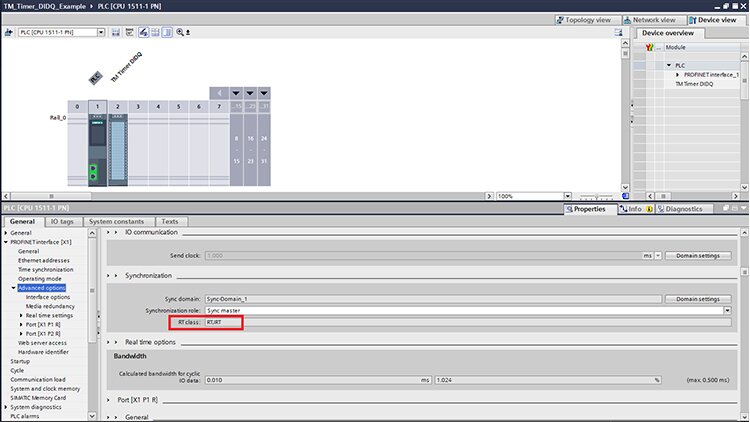
Click on the image for higher resolution
In a project, if you attempt to use the high-speed functionality of the module when the device is configured on the local rack, often your technology object (such as a Measuring Input, Output Cam, Cam Track, etc.) will throw a vague error such as Configuration.
If you see this error and are trying to use the special high-speed functions of a Siemens TM Timer DIDQ Module, confirm that the device is not configured locally to the CPU.
TM Timer DIDQ Module as Remote I/O
When mounted on a remote rack, the CPU and Head Module (such as an ET200MP) can communicate via high-speed IRT Profinet. For a quick, simple explanation of how IRT works, check out this press release from Siemens.
In most of the technical documentation and examples that Siemens provides about the TM Timer DIDQ modules, the modules are used in a distributed I/O system. The Timer module is mounted not with the S7-1500 PLC, but on a remote rack with a communication head module as shown in the hardware configuration views below. Here is more technical information on the hardware and an example project.
In these sorts of configurations, the full functionality of the TM Timer DIDQ module can be realized. This includes:
- Timestamp acquisition (Timer DI)
- Time-controlled switching (Timer DQ)
- Counting
- Pulse width modulation (PWM)
- Oversampling
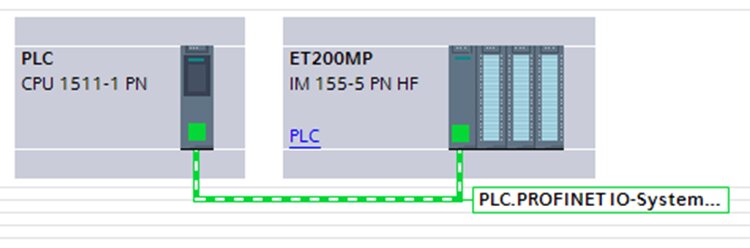
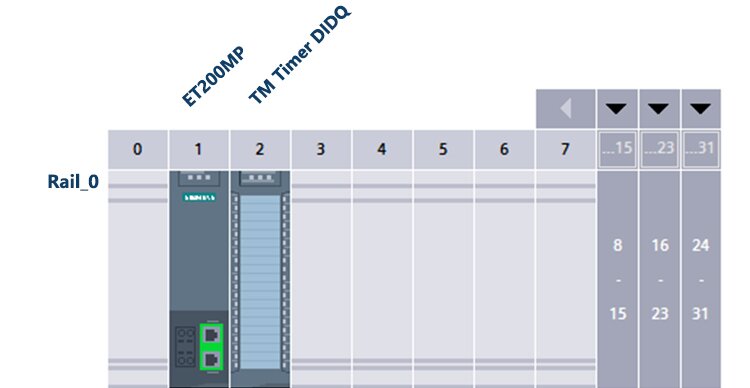
Once the head module and TM timer module are added to a remote rack, the device can be configured as an IRT I/O device as a sync slave.
Configuring the Device
- From the Network View of your project, select the appropriate Profinet connection and open its Properties.
- Select Domain management > Sync domains > Sync-Doman_1 > Device.
- In the IO system table, ensure that the PLC is listed as the Sync Master.
- In the IO devices table, ensure that the RT class of the PLC can be either RT or IRT and that the Synchronization role of the PLC is Sync master.
- Also in the IO devices table, select IRT as the RT class for the ET200 device and set the Synchronization role to be Sync slave.
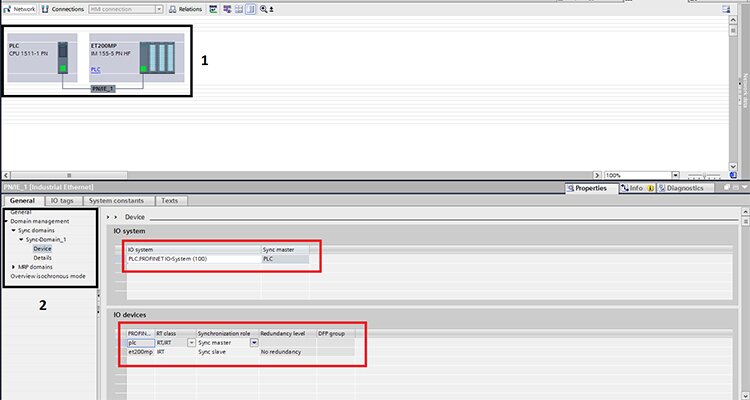
Click on the image for higher resolution
With this hardware configuration, it will now be possible to use the high-speed I/O features of the Siemens TM Timer DIDQ module!
Here is an example to follow with more detailed, step-by-step instructions to configure the technology module in TIA Portal.
Check out this post, Relative Gearing to an External Encoder with a Siemens 1500 PLC, to learn more pro-tips for TIA Portal or head over to the Siemens S7 PLC Programming and Motion Control Engineering and Servo Systems sites to get a better idea of what DMC can do!